Diaphragm pistons aka Rolling Diaphragm Actuators are pneumatic or hydraulic pistons which use a flexible rolling diaphragm instead of a conventional sliding seal. There's a few millimeters of clearance between the piston shaft and the bore, and the diaphragm wraps tightly around the shaft in that space. Somewhere along the length of the piston the diaphragm arcs smoothly away from the shaft to the larger diameter of the bore in a half-donut shape.
When the piston moves this half-donut rolls between the shaft and the bore without any sliding friction. It's the same mechanism as taking off a tight pant leg or sock: At the rolling edge the pants flip inside out and start moving, but all the fabric lower down your leg is just sitting there. Except, here there's pressure on the inside side of your donut, so the inside out part of the diaphragm is stretched to the diameter of the outer bore instead of rubbing against the section remaining on the inner bore.
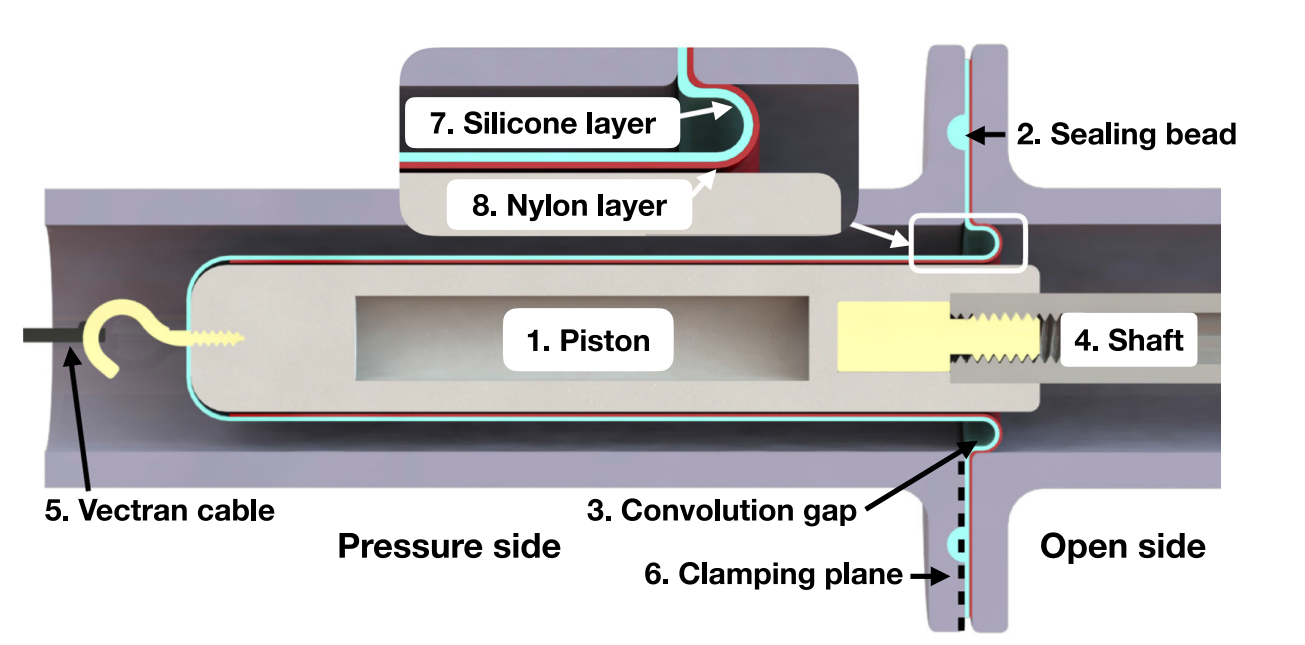
Rolling is generally much, much smoother than sliding (see the Archimedes Drive for another example) and that holds true here. Diaphragm pistons have exceptionally low hysteresis which makes them great for precise motions and teleoperation systems. A properly designed diaphragm piston also has high cycle life without any maintenance or lubrication.
These actuators are exciting to me for two reasons: First, they're very DIY friendly. The tolerances are so loose, I'm pretty sure you could make serviceable actuators with hand tools. Second, they're a bit of a withered technology in that they've been around a while but they're still too niche to merit a Wikipedia page, and I think they're going to see a renaissance soon. Simple old tech that might soon go screaming down its learning curve will always hold a special place in my heart.
I think we're going to see these used a lot in biomimetic robots and human-robot interaction problems. Disney Research has a great teleoperation demo using them to safely play with kids, and this paper has great fabrication instructions for a long stroke version meant for surgical teleoperation in an MRI machine.
I'm fascinated by the idea of reconfiguring fluid mechanical transmissions using low hysteresis actuators like this and relatively low power electronics. A long time ago I worked on 3D printed prosthetics where there's this interesting trade-off between body-harness power and electronic actuators. The body harnesses use the wrist, elbow, or shoulder motion of the wearer to pull a cable which acts like a tendon and makes the hand "grasp." It's a cheap and effective system but the sleeved cables they use have a lot of hysteresis and low efficiency, both of which make fine manipulation more difficult. If you just replaced the cable with a pair of diaphragm pistons and a water line the grip strength of the hand would ~double and the wearer would have fine grained control over it. However if you went on to add a valve complex, more output pistons, and myoelectric sensors to command the valves you'd move into proper bionic territory. If you fill a hydraulic actuator with water and then seal its valve the actuator holds its position, so you could switch modes, adjust say your thumb position and then leave it there while you go about your day. You could add pressure regulators to force-limit the hand in some modes. Essentially, water pressure in a bunch of low-hysteresis actuators is a more fungible form of work than cable tension, so you're free to add all sorts of wonderful capabilities.